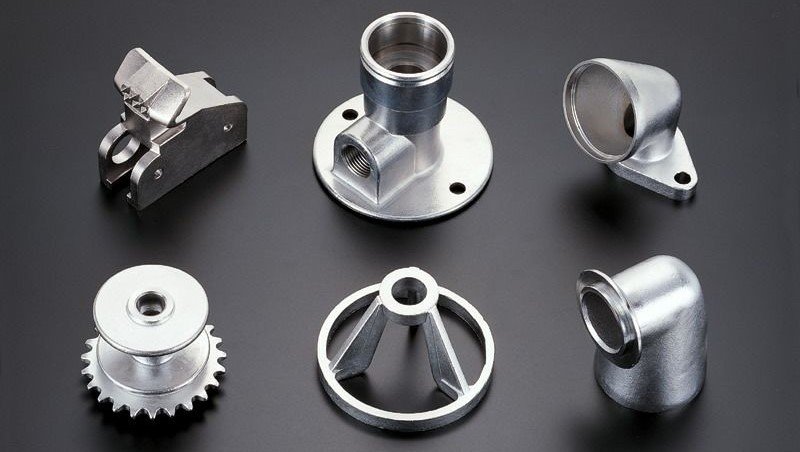
Have you ever wondered how those intricate, highly detailed metal pieces in machinery came to life? The answer is extremely enthralling. Welcome to the world of Zinc Die Casting.
Zinc Die Casting is a manufacturing process that involves molding molten zinc alloys into high-precision components, That is, involving melting zinc alloys (hence the name zinc alloy die casting) and injecting it into a ready-prepared die casting mould. This highly versatile and economical process is known for delivering parts with superior finish and dimensional accuracy.
Let’s delve further into the fascinating details of zinc die casting and its significant industrial implications.
What is the Zinc Die Casting Process?
Zinc Die Casting follows a series of precise steps.
Initially, the zinc alloy is heated until it liquefies.
The molten metal is then injected into a steel die, or mold, under high pressure.
Once the alloy solidifies, the mold is opened to eject the part.
These steps can be repeated thousands of times before the mold needs to be replaced, making this process highly efficient for mass production.
What Zinc Alloys are used in Die Casting?
Zinc alloys used in die casting include ZAMAK alloys and the Zamak family’s latest addition, ACuZinc.
These alloys are valued for their excellent strength, hardness, and elasticity. Furthermore, their ability to maintain dimensional stability, even under extreme conditions, is noteworthy.

What are the Advantages and Disadvantages of Zinc Die Casting?
Zinc Die Casting provides numerous advantages, such as high precision, high-speed production, and the ability to produce complex shapes with thin walls.
Additionally, the resultant components are highly durable and have a long life span.
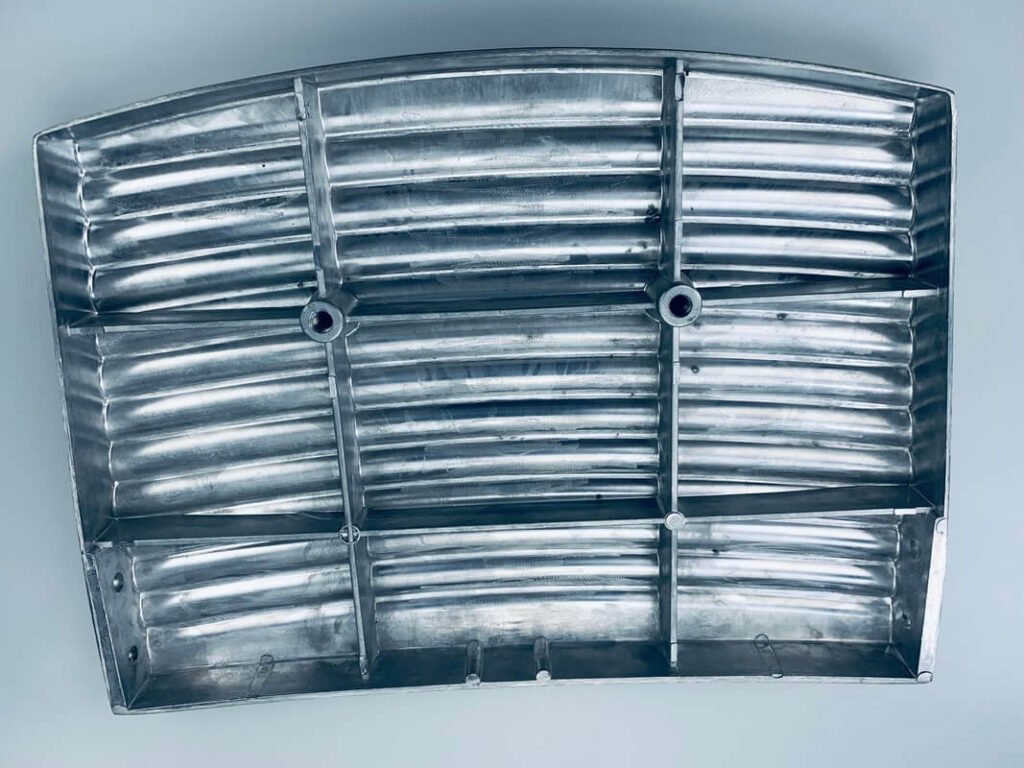
However, this process does have a few disadvantages. While Zinc alloys are more cost-effective than other materials, they can be more expensive than some plastics. Furthermore, over time, exposure to certain environments can cause zinc components to corrode, although this issue can be mitigated with appropriate finishing techniques.
Where are Zinc Die Castings used?
Zinc die castings are used extensively across industries due to their versatility.
Applications include machine parts, automotive components, and hardware metal parts for furniture and kitchen cabinets.
How Zenhite Harnesses Zinc Die Casting
Zenhite Hardware employs Zinc Die Casting to produce an array of hardware metal parts. We offer custom solutions tailored to our client’s unique needs across various industries, underscored by our commitment to quality control, technical support, and competitive pricing.

Why Choose Zenhite for Zinc Die Casting Needs?
Zenhite is the go-to choice for clients valuing quality, durability, and competitive pricing. Our comprehensive technical support empowers clients to make informed decisions that best meet their equipment needs. Our mission is to continuously extend our reach to serve more clients in need of top-quality hardware equipment.
Conclusion
Zinc Die Casting is a powerful manufacturing process that offers a host of benefits, from precision to cost-efficiency. Trust in Zenhite for superior quality and tailored service in all your Zinc Die Casting requirements.