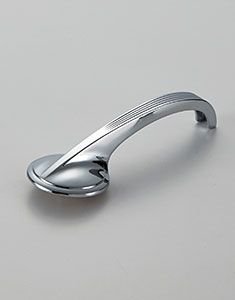
When I first learned about the zinc alloy die-casting process, I was honestly blown away by how precise and efficient it is. You might think, “How hard could it be to make a handle?” But trust me, there’s a lot more going on behind the scenes than you’d expect. Let’s dive into it!
Step 1: Melting the Zinc Alloy
It all starts with melting down the zinc alloy, which is a mixture of zinc and other metals like aluminum, copper, or magnesium. The goal is to create a molten metal that can be shaped into a handle. What’s really cool here is that zinc melts at a lower temperature compared to other metals, so the energy required is significantly less—making it an efficient and cost-effective process. This is why zinc alloy is a favorite in industries like hardware manufacturing. It’s strong but also relatively easy to work with in its molten state.
Step 2: Pouring the Molten Metal into a Die-Cast Mold
Once the zinc alloy reaches the perfect molten state, it’s time to pour it into a die-cast mold. These molds are precisely designed to give the handle its final shape. Imagine a perfectly crafted mold with intricate details—every curve, bevel, and notch of the handle is planned out in advance. This is where the magic happens. The mold can be used over and over again, allowing manufacturers to produce handles consistently and at a high volume. This repeatability is one of the huge advantages of die-casting, especially when you’re making thousands of identical parts.
What blew my mind here is the difference between hot-chamber and cold-chamber die-casting. In the hot-chamber method, the molten zinc alloy is drawn into the mold quickly, which is ideal for materials like zinc with lower melting points. It’s faster and perfect for mass production. On the other hand, the cold-chamber method is slower because the molten metal has to be manually transferred into the mold—this method is more commonly used for metals with higher melting points like aluminum. For zinc, the hot-chamber die-casting process is the go-to choice.
Step 3: Cooling and Hardening
Next, we come to the cooling phase. Once the molten metal fills the mold, it starts to cool and harden into the shape of the handle. This part of the process happens relatively fast with zinc alloy because, again, its lower melting point speeds up cooling. Manufacturers typically use high-pressure cooling techniques to make sure the handle solidifies without any air pockets or cracks—nobody wants a weak, brittle handle!
Here’s the thing: if the temperature isn’t controlled perfectly, it can lead to some serious defects. I remember reading about a project where a batch of handles had tiny air bubbles trapped inside because the cooling process wasn’t optimized. These defects might not be visible right away, but over time, they can cause the handles to break or wear down faster. Quality control at this stage is crucial.
Precision and Repeatability
One of the best parts about die-casting is the precision. Every single handle comes out identical to the last, down to the smallest detail. This level of consistency is why die-casting is such a popular method for manufacturing handles at scale. Once you’ve set up the mold and dialed in the process, you can produce high-quality, durable zinc alloy handles in large quantities without any significant variation between products.
Differences Between Hot-Chamber and Cold-Chamber Die-Casting
I’ve touched on this briefly, but it’s worth reiterating because the method you choose can impact production speed and cost. Hot-chamber die-casting is typically faster and more efficient for zinc alloy, but cold-chamber die-casting is necessary when dealing with metals like aluminum. Each process has its own advantages depending on the material being used, but for zinc alloy handles, hot-chamber die-casting wins hands down.
What’s fascinating to me is how something so simple—a handle—can come from such a detailed and technical process. The next time you grab a cabinet handle, just think of all the engineering and design that went into making it! The die-casting process isn’t just about forming metal, it’s about creating precision, durability, and repeatability, which is why zinc alloy handles have become such a staple in homes and businesses around the world.